Our Competencies
Scientific research work
The engineering school and scientific developments of the best Russian technical universities in the field of vehicle transmissions form a powerful foundation for the creation of fundamentally new automatic transmissions as well as innovative hybrid and electric transmissions. We begin our research at the level of theoretical insights and program calculations, which are then confirmed by mandatory experiments using our own bench equipment. If a wider research program is needed, our specialists work in close cooperation with highly qualified Russian and foreign partners with a worldwide reputation, allowing us to offer our customers a comprehensive and verified solution. Our team includes 7 doctors and candidates of engineering sciences who carry out active research and project activities, which is confirmed by the publication of 35 scientific articles and the receipt of 60 Russian and international patents for invention. Our accumulated practical experience along with extensive theoretical knowledge allow us to face the future with confidence and successfully use the obtained research results in various projects.
Development of automatic transmissions
KATE was founded on the basis of the experience of Russian design engineers working in the field of repair and maintenance of automatic transmissions for cars. Ideas for improving the design, new kinematic schemes, and innovative solutions for the launch device were implemented in the course of the first projects to improve the automatic transmissions. The extensive experience and comprehensive expertise gained by our specialists in the process of working on these projects allow for high-quality and work at all stages of product development, and a large number of patents and implemented unique solutions indicate a high level of professionalism of our team as an independent and advanced developer of new-generation automatic transmissions. Our specialists annually participate in international transmission symposia and scientific conferences in Germany and China, keeping abreast of all the latest trends in the industry, and exchanging experience with foreign colleagues during topical discussions and reports. We are prepared to fulfill challenging tasks and implement the latest solutions within the design of modern automatic transmissions featuring high competitive advantages.
Development of transmission elements
Hybrid and electric vehicle transmissions are the most promising solution in the context of increasingly stringent environmental regulations for transport in large metropolitan areas all over the world. Experience in designing planetary gearboxes enabled KATE to start actively working in this promising area from 2013 onwards, and successfully pass the entire product development cycle from the TOR setting to the serial production stage for the 2-speed transmission of the electric bus. The use of modern design schemes and the exchange of experience with technical institutes and partners allows our company to design virtually the entire range of transmission units for cars, trucks and buses. We are ready to fulfill challenging tasks and implement the latest design solutions.
Experimental production
Manufacturing and assembling prototypes of new products is a very time-consuming process that requires the participation not only of highly skilled assemblers but also of design engineers, technologists, and quality assurance representatives, since all the deficiencies identified during assembly must be documented for the subsequent adjustment of detailed design and technological documentation. The production site located in Moscow is equipped with all the necessary modern equipment and tools for assembling prototypes and batches of new products and for installing them in cars. This site allows us to perform works in as short a time as possible and to a high standard, directly influencing the development process; this includes preparing the facilities before starting tests, scheduled inspections and re-assemblies to make the necessary changes, including for the purposes of design studies. Our own mobile repair shop supports road tests at the test track in order to improve the development schedule. The employees of our experimental production have many years of experience and are ready to perform all the work mentioned.
Bench tests
Bench tests clear the way for the newest automobile units to the market. We develop test programs and procedures, prepare the test object, and conduct a wide range of bench tests of parts, components, and the products themselves, making use of a variety of test equipment, sensors, data collection and processing systems. These include hydraulic test rigs to verify electrohydraulic components and systems; no-load high-speed benches to carry out performance tests; tilting research bench of the tested unit to verify the performance in the entire range of angles of vehicle movement; load bench with a high input torque and input shaft rotation speed, which allows to simulate real modes of vehicle movement.
Field tests
All our developments at the prototype stage pass mandatory within-car tests. We develop road test programs and methods, prepare the test object, and conduct tests in full. All works are carried out on a special test track in Podmoskovye, designed for all kinds of road tests: 15 types of various routes and pavings with a total length of 110 km over a total area of 25 km² with the possibility of conducting works in winter and in summer. The different types of roads and terrain within the same grounds significantly reduces the time for debugging the operation of the unit in the car. Test drivers together with engineers can work in several shifts, and our own mobile repair shop supports road tests at the test track in order to improve the schedule. Based on the results of the tests, the product is adapted, improved and refined as necessary, starting from the very first prototypes to serial products, and the control system is developed and calibrated for automatic transmissions, hybrid and electric transmissions. If you are interested in carrying out these works, please contact us for further details.
Mass production
Mass production of automatic transmissions with a total capacity of up to 180,000 items a year, which is being prepared for launch in Kaliningrad, will be advanced in the field of assembly of automotive components. A modern assembly line with a number of special tools and control/test benches at each assembly stage will allow for manufacturing and testing modern serial innovative car components and systems.
The serial production will include:
- logistic areas, where the parts received from suppliers will be accumulated;
- site for cleaning and preserving parts and assemblies;
- technical control department equipped with modern manual and automated control means, control and measuring machine, hardness meter, profile meter, and other advanced measuring instruments;
- machine-tool area for the main components of automatic transmissions – gear wheels, carriers, shafts, drums, coupling components;
- a modern automated assembly site, equipped with electronic means of operational control and assistance to the assembler; this site will be the main one.
Our own large test site for finished products and an extensive warehouse will make it possible to provide customers with an uninterrupted supply of quality units in the agreed time. We are also open to cooperation with automakers and their suppliers in the field of localization of production within the Russian Federation and are ready to begin production of the required automotive components at our production site.
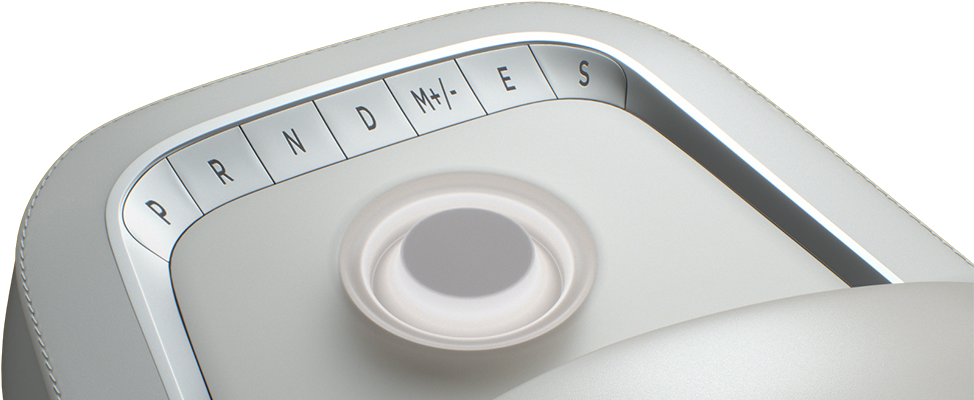
